Have you ever thought that supply chain management can be automated and errorless in some way? Or less involvement of human efforts?
Indeed, a tough call as it requires management of Material Requests from different Retail Partner shops, Stock Pickup Notes for those Materials Requests, and Warehouse management.
One Promising and Prominent tech-enabled grocery retail chain for small towns and they have more than 50+ Grocery Stores in the network; Our Client was searching for an ERP solution that must be easy to use, SCALABLE, AGILE, and ROBUST. They are a fast-growing startup that is building a branded retail chain by upgrading individual stores similar to how OYO has organized the hotel industry.
The team comes from a distinguished background in terms of experience and educational qualification. After conducting multiple research and analyzing different ERPs, they choose ERPNext as their Digital solution as it’s AGILE, easy to customize, and ROBUST.
All the Grocery Stores create Material Requests for the Our Client to get the items delivered. All the Material Requests are automatically added to Our Client’s ERPNext System. Every day our client receives more than 1000+ Material Requests from different grocery stores.
Here, We have developed a Data Processing Tool which bifurcates items in the item group and creates Picking Requests. It also auto-assigns Picking Requests to available Picker.
Available Picker picks the Items and prepares the Item container. Once the Item container is ready, they compare the Picking Lists and Items in Second Verification.
The key feature here: We all know that sometimes we forget to buy some items when we visit grocery stores. And, indeed, it also becomes difficult for pickers when the list is long. Here, we created one visual and noticeable functionality for pickers.
If picked products will be indicated as green and the remaining products will be indicated in red. So the chances of missing a product are zero and here we are making it efficient for the pickers and eventually for all.
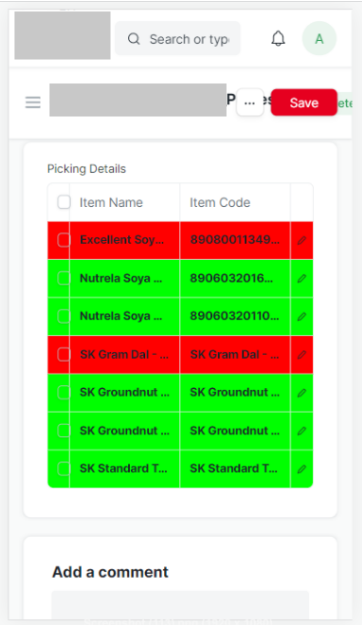
After successful second-time verification, they send it to the Dispatch Manager, where he creates the Delivery Note and attaches it with the Item Container and despatch it to the respective Stores.
Stores check whether items are as per the Material Requests or not, if it’s as per the Material Request, they accept it and close the cycle. Otherwise, they return back it to Our client.
The key feature: Historical Purchase Price and the Current Price Indicator.
Having a record indicator that contains the historical data and indicates the difference from it, makes life easy for the decision-makers. So, as per the request, we have provided the visual and notable functionality in which we can see different colors; yellow, red, and green.
- If the item price is the same as per the last purchase, it will remain YELLOW.
- If the item price is higher than the last purchase, it will indicate RED.
- If the item price is lower than the last purchase, it will indicate GREEN.
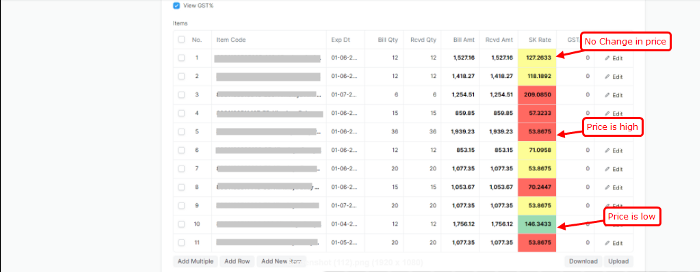
Who are we?
Akhilam Inc. is a diverse team of ERP and ERPNext Consultants, Developers Professionals with an infinite mindset and a collaborative culture.
We at Akhilam believe Successful ERP Implementations certainly drive overall process efficiencies and innovation in Business. And, A well-integrated ERP system allows for more accurate information, reducing risk in operational activities and allowing for improved forecasting in Business.
Our AGILE Approach: Leverage agile frameworks to provide a robust ERP. Iterative approaches to ERP implementation with collaborative thinking with all the Stakeholders to deliver the next generation Efficient, Ease to Use ERP that drives Business.
Do you want to drive your business with Digital Transformation? Drop us a mail — shivam@akhilaminc.com or raaj@akhilaminc.com